Unlocking the Potential of Ultem: A Game Changer in 3D Printing
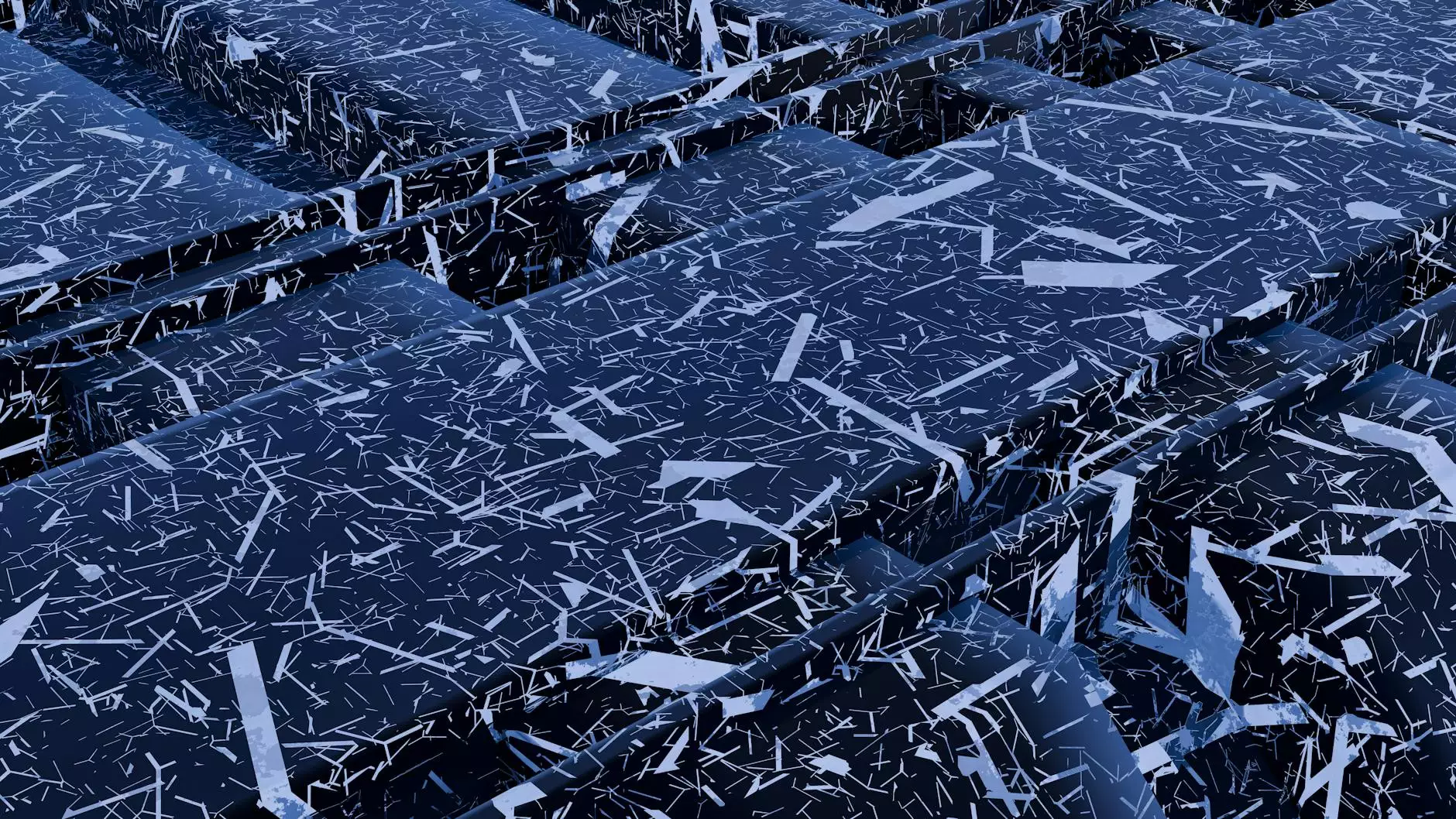
In the world of advanced materials, few have made as significant an impact as Ultem. This high-performance thermoplastic, known scientifically as polyetherimide (PEI), is reshaping industries, particularly in the realm of 3D printing. With exceptional strength, heat resistance, and electrical insulating properties, Ultem is becoming the preferred choice for professionals seeking durable and reliable materials.
Understanding Ultem: Composition and Characteristics
Ultem, a registered brand of SABIC, is celebrated for its unique chemical structure that grants it superior qualities. The molecular design of Ultem allows it to withstand high temperatures while maintaining excellent mechanical properties. Here are some of the standout attributes:
- High Strength-to-Weight Ratio: Ultem provides remarkable strength while being lightweight, making it ideal for applications where reducing weight is critical.
- Thermal Stability: With a glass transition temperature of approximately 217°C (423°F), Ultem maintains its shape and strength at elevated temperatures.
- Chemical Resistance: It is resistant to a variety of chemicals, making it suitable for challenging environments.
- Electrical Insulation: Ultem exhibits excellent dielectric properties, which is essential for electronic applications.
- Biocompatibility: Certain grades of Ultem are biocompatible, which is beneficial for medical applications.
The Role of Ultem in 3D Printing Technologies
In recent years, 3D printing has revolutionized manufacturing by enabling rapid prototyping and production of complex geometries. Ultem has emerged as a favored material in this domain due to its compatibility with various 3D printing processes, particularly Fused Deposition Modeling (FDM) and Selective Laser Sintering (SLS).
Fused Deposition Modeling (FDM) with Ultem
FDM is one of the most popular 3D printing techniques, and the ability to print with Ultem brings numerous advantages:
- Robust Functional Prototypes: Ultem's strength allows engineers to create prototypes that can withstand functional testing and real-world applications.
- High-Temperature Applications: When printed with Ultem, parts can endure extreme temperatures, making them suitable for aerospace and automotive industries.
- Complex Geometry Creation: The thermoplastic can be extruded in fine layers, allowing for intricate designs that traditional manufacturing methods cannot achieve.
Selective Laser Sintering (SLS) with Ultem
Another revolutionary method, SLS, applies a laser to sinter powdered material, forming a cohesive structure. The benefits of using Ultem in SLS include:
- Enhanced Design Freedom: SLS allows for components with complex geometries that reduce weight without sacrificing strength.
- Optimized Mechanical Properties: Parts printed with Ultem exhibit excellent impact resistance and tensile strength.
- Fast Production Rates: SLS technology enables quicker production cycles, making it easier to meet tight deadlines in industrial settings.
Applications of Ultem in Various Industries
The versatility of Ultem extends across multiple industries, showcasing its adaptability and performance. Below are some notable applications:
Aerospace and Aviation
In aerospace, the need for lightweight yet strong materials is paramount. Ultem is utilized in:
- Interior Components: From control panels to seating systems, Ultem's resistance to high temperatures and flame-retardant properties make it ideal.
- Functional Parts: Engine components and structural parts that require lightweight materials with exceptional strength.
Automotive
The automotive sector is continuously searching for ways to improve efficiency and reduce weight. Ultem contributes by:
- Electrical Components: Ultem’s electrical insulating properties are invaluable for wiring and connectors.
- Engineered Components: Parts that are exposed to high heat and require high performance during operation.
Medical Devices
Ultem is increasingly making its mark in the medical field due to its biocompatibility and robust qualities:
- Surgical Instruments: Durable and sterilizable, Ultem is favored for tools that need to withstand rigorous cleaning processes.
- Implants: Certain grades of Ultem can be used for temporary implants or devices due to their strength and compatibility with bodily tissues.
Advantages of Using Ultem in Manufacturing
Employing Ultem for manufacturing not only fulfills technical requirements but also offers various economic and operational benefits:
- Cost-Effectiveness: Although Ultem can be more expensive than other thermoplastics, its durability reduces the need for frequent replacements.
- Reduced Production Time: The ability to create complex geometries without extensive tooling helps to streamline production timelines.
- Sustainability Benefits: Utilizing Ultem in 3D printing reduces waste associated with traditional manufacturing methods.
The Future of Ultem in 3D Printing
As technology continues to advance, the potential for Ultem in 3D printing seems limitless. Companies are investing in research to develop new grades of Ultem that enhance its properties further, making it an even more attractive option for various applications:
- Improved Formulations: Ongoing development in polymer science aims to produce Ultem variants with enhanced thermal or mechanical properties.
- Integration with Smart Technologies: The future may see Ultem being combined with sensors or other technologies to create smart components that can monitor their environments.
Conclusion
Ultem is not just a material; it is a game changer in the field of 3D printing and beyond. Its combination of exceptional properties, coupled with a wide range of applications across industries, makes it a material of choice for innovative designers and engineers. By embracing Ultem, companies like Infotron are not only enhancing performance but are also positioning themselves at the forefront of technological advancements. As the industry moves towards more sustainable and effective solutions, the role of Ultem will undoubtedly expand, leading to even greater innovations in the years to come.